The Chicken, the Egg, and the Missing Incubator of Textile Recycling
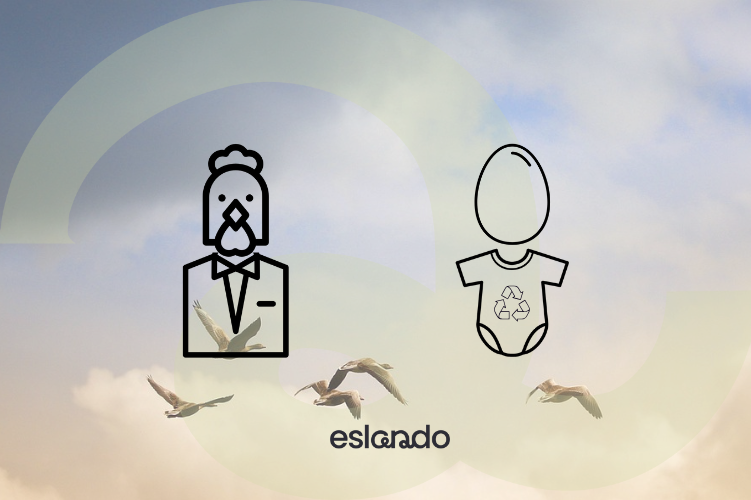
The fashion & textile industry is at a crossroads. On the one hand, we are producing more textile waste than ever before. On the other hand, new technologies are emerging that can recycle used clothing back into raw materials, creating the possibility of a truly circular textile economy.
So why hasn’t textile recycling gone mainstream?
This is often described as a chicken-and-egg problem: Should we collect more waste first, build more recycling plants, or wait until markets mature before scaling the system?
At Eslando, we believe this isn’t just a sequencing issue — it’s a strategic one. And solving it begins by recognising what’s missing at the heart of the system: sorting.
Without sorting, recycling ends up as scrambled potential. We’re trying to hatch a circular system — but the incubator of sorting is missing.
What the System Looks Like Today
The current system is fragmented. Textile waste collection is inconsistent and rarely standardised. In many regions, post-consumer textiles are co-mingled with household waste or collected for reuse and resale — not for recycling.
Meanwhile, a growing number of innovative recyclers (mechanical, chemical, and enzymatic) are ready to scale. But despite this technical readiness, many of these facilities operate below capacity. Why? Because they struggle to access the right feedstock — waste that is sorted by fibre type, colour, blend, and contamination level.
Simply put, you can’t recycle what you can’t sort. Without the right infrastructure, textile recycling will never gets the chance to hatch.
🥚 The Egg: Recycling Technology
A lot of the funding to date has gone into building recycling plants — chemical, mechanical, and enzymatic. But the catch 101 is: Recycling tech can’t scale if it doesn’t have reliable, clean feedstock.
Today, most recycling plants (even the big ones) operate below capacity because they can’t get enough of the right material- sorted by fibre, colour, blend, contamination, etc.
Without feedstock, the recycling plants are expensive, idle assets.
Without sortation and collection, they’re solving the wrong end of the pipeline.
🐣 The Chicken: Collection
It seems logical to start at the beginning — just collect more waste.
But the reality is: We already have enough collected textile waste, about 750k tonnes in the UK and 1.7 million tonnes in the EU.
The real problem here is: we don’t have data-rich, pre-sorted, recycler-ready textile feedstock.
Today’s collection systems are often municipal, charity-based, or export-driven. They’re designed for reuse or landfill diversion, not for fibre-level recycling.
Throwing more money at “collection” without redesigning it for circularity will just create a bigger mess.
“If we collect any more textiles without an economical exit route such as recycling, then the collectors will go bankrupt.”
The Critical Role of Sorting
Sorting sits between waste collection and recycling. It’s the part of the system that makes everything else work — and yet it’s often overlooked in funding, policy, and infrastructure planning.
Recyclers need uniform, high-quality inputs. Collectors need viable markets for what they collect. Brands need traceability and confidence in their recycled content claims.
Sorting is the layer that makes all of this possible. Or in other words sorting is the nest where we can lay our recycling eggs.
Without it, textile waste remains a low-value, high-risk commodity — often ending up in landfill or incinerators, even when the intent is circular.
Manual vs Automatic: A very wide Gap in Sorting Capacity
In countries like India, and parts of Eastern Europe & USA, the textile recycling ecosystem is already more active — not necessarily because of better policy or technology, but due to greater labour availability and lower operational costs
Countries like India or parts of Eastern Europe have longstanding informal systems, where waste is sorted by fibre type or garment category and directed to mechanical recyclers — many of whom are already operating at commercial scale. Manual sorting may lack precision, but it has enabled these regions to extract material value from textile waste at volumes the West is still struggling to process.
On the other end of the spectrum, countries like the United States have built large-scale collection infrastructure- often initially enabled by cheap, often immigrant labour, especially in regions like the Southwest. These facilities supplied inputs to downstream industries like insulation, wiping cloths, and rags. However, as wages rise and material demand shifts, many of these facilities are now transitioning to automation, investing in sensor-based sorting and robotics to serve higher-value markets like textile-to-textile recycling. The collection facilities already has the funds to invest in automation.
The UK and parts of Western Europe sit somewhere in the middle — with high labour costs but without widespread investment in automated sorting infrastructure. As a result, large volumes of collected textile waste cannot be economically sorted to recycler-grade quality, limiting the viability of downstream recycling solutions.
The challenge is no longer about collecting more waste — it’s about processing what we already have, in the right way, and with the right infrastructure. Manual systems may be efficient in the short term, but the future of textile recycling — especially for complex fibre blends — will depend on automation, data, and design for circularity from the start.
But Advanced Sorting is Expensive — And Economically Fragile
Here’s the challenge: building advanced sorting facilities is not cheap. A high-tech plant equipped with robotics, fibre detection, and automated classification can cost upwards of £1 million in capital expenditure. That’s a significant investment for any waste operator, especially when the revenue model for sorted textile waste is still uncertain.
Many recyclers can’t yet commit to high, stable prices for feedstock. Brands often run short-term pilots rather than long-term procurement contracts. As a result, the economics for sorting facilities — even though they are critical — are difficult to justify without external support or cross-sector collaboration.
It’s a classic “chicken-and-egg” dilemma:
We need sorting infrastructure to scale textile recycling.
But we need recycling demand and price guarantees to justify investing in sorting.
Don’t put all your textiles in one basket — unless that basket is well-sorted 😉.
So, What Comes First?
The industry is circling the coop, but still afraid to jump. Our view is clear: sorting must come first.
Investing in sorting infrastructure unlocks value throughout the system:
- Recyclers can access consistent, high-quality inputs
- Collectors can be paid based on quality, not just weight
- Brands can access traceable, verifiable recycled fibre
- Policymakers can build effective EPR systems around clear waste flows
In other industries — from metals to PET bottles — this “missing middle” is what made recycling viable. Textile waste is more complex, but the logic remains the same: without standardised, recyclable inputs, circularity cannot scale.
Lessons from Other Industries: Sorting Comes Before Scale
The textile industry isn’t the first to struggle with this chicken-and-egg dilemma. Plastic bottles, aluminium, and paper recycling all went through similar phases of inefficiency — and all reached scale only once sorting systems were standardised and centralised.
Take the case of PET bottle recycling. In the early 1990s, recyclers faced massive challenges: bottles were collected inconsistently, contaminated with labels and food waste, and hard to separate by polymer type or colour. The solution wasn’t just building more recycling plants — it was investing in high-speed, automated sorting lines that could identify and separate PET at scale. This gave rise to a predictable, high-quality feedstock stream that made large-scale chemical and mechanical recycling commercially viable. Today, PET bottles are one of the most successfully recycled materials in the world (a recycling rate of 75% recycling rate for sorted PET bottles). About 8 million tonnes of fibres produced as a result of PET bottle recycling are used in textiles every year.
Similarly, in paper recycling, progress didn’t accelerate until collection systems began to separate newspapers, cardboard, and mixed office paper — turning them into distinct, marketable grades. Only then did paper mills begin to confidently invest in reprocessing infrastructure.
The key takeaway: recycling becomes viable only after sorting becomes standardised. Not the other way around.
The Path Forward
To make sorting infrastructure viable, here is what the industry could do:
- Brands need to move from pilots to multi-year commitments for recycled content.
- Policymakers need to fund sorting and enforce recycled content targets under EPR.
- Recyclers and collectors need platforms like Eslando to match supply and demand.
- Investors need to support both physical and digital infrastructure with patient capital and blended finance models.
Closing the Loop Starts with the Right Connections
At Eslando, we believe that solving the chicken-and-egg problem of textile recycling requires more than infrastructure — it requires coordination.
Our digital marketplace is the infrastructure layer that connects pre-sorted textile waste with the right recyclers, making material flows visible, traceable, and tradeable. Whether you’re a recycler seeking consistent, high-quality feedstock, or a supplier, collector, or trader with sorted textile waste ready to sell, Eslando helps you move material faster, more transparently, and with confidence.
We’re building the engine that powers circularity at scale — One match at a time.
📩 Get in touch to learn how we can help you trade textile waste more efficiently and build the future of circular textiles.
Let’s stop egg-specting the system to fix itself — and build the infrastructure to make it fly.